Overview
empirical faced a unique challenge with their TRD warehouse in Dakota Dunes, NE. Originally equipped with an automated storage and retrieval system (AS/RS) built by a competitor, the system struggled to meet the company’s needs. empirical turned to Westfalia to retrofit and optimize the facility. The solution transformed an underperforming AS/RS into an efficient, state-of-the-art system designed specifically to handle empirical’s complex order fulfillment requirements. Westfalia approached the challenge, customized the solution, and delivered exceptional results.
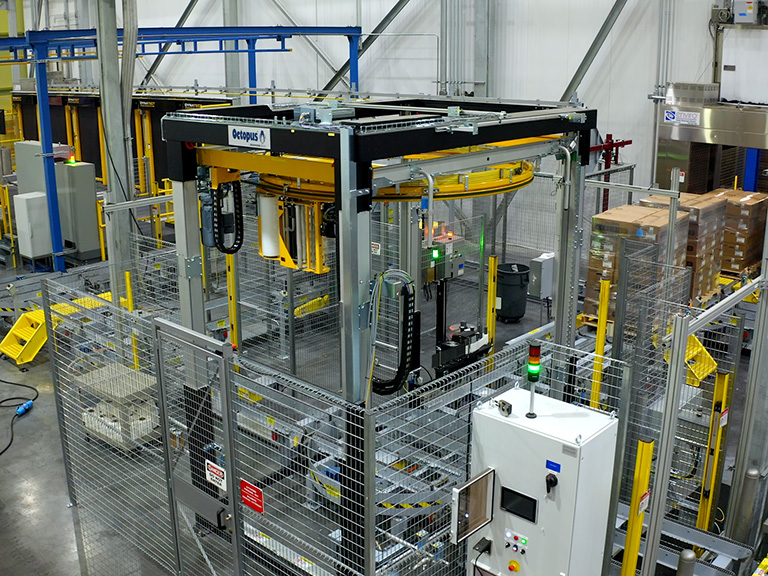
Challenge
The original TRD warehouse AS/RS was not functioning as expected. Designed and installed by a competitor, the system had significant issues, resulting in a prolonged two-year commissioning process that ultimately failed. empirical needed a reliable solution to handle their growing operations, which included the production of multiple beef products such as primal cuts, ground beef, and taco meat. Their existing system was not optimized for the variety of products or the specific requirements of their order fulfillment, which included precise picking based on fat content, weight, and quality.
The warehouse rack system, a two-rail setup, was also different from the typical three-rail systems used by Westfalia. empirical needed a partner who could work within these constraints without requiring a complete overhaul of the racking infrastructure.
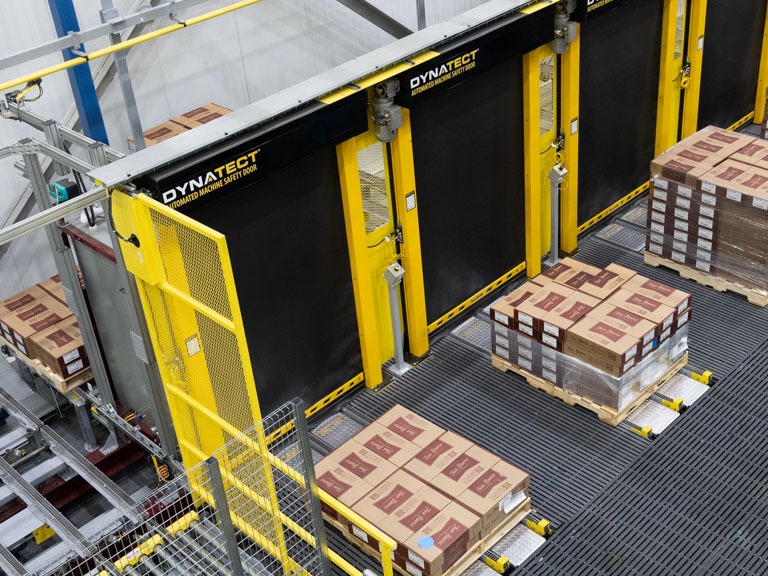
Solution
Automated Warehouse Solutions Westfalia leveraged their extensive expertise in automated systems to retrofit the TRD warehouse, replacing the existing conveyors, cranes, and software while retaining the original rack system. The core of the solution involved Westfalia’s Savanna.NET® software, which was integrated to manage the entire operation seamlessly. Westfalia installed customized cranes and conveyors designed specifically to fit the non-standard rack structure, ensuring minimal disruption and cost savings for empirical.
Additionally, Westfalia incorporated a goods-to-person (GTP) picking system to address the complex picking requirements of empirical. This system allowed for precise order fulfillment, accommodating multiple criteria such as fat percentage and weight range, and minimized manual handling, thus increasing efficiency and accuracy. The design also included strategic staging lanes to buffer product flow and ensure smooth operations during high-demand periods.
System Features
AS/RS footprint: 15,000 sq. ft.
AS/RS pallet storage: 10,000+ positions
Storage: Up to 9-deep storage lanes with a redundant middle block
Outbound order staging: Multi-lane staging
Two (2) customized storage/retrieval machines (SRMs) in two (2) aisles, 9 levels high
Goods-to-person (GTP) picking system with two (2) pick stations.
Automated pallet conveyors and integration
Temperature control: refrigerated and frozen product handling
Backup power system and enhanced safety protocols
Savanna.NET® Warehouse Management System (WMS) with seamless integration for real-time data
The new system drastically improved picking efficiency. The GTP system allowed Empirical to fulfill orders faster and more accurately, meeting specific customer requirements with ease.
Westfalia’s cranes and customized solutions enabled Empirical to maximize the use of their existing rack system, achieving higher storage density without the need for costly rack replacement.
By replacing the unreliable equipment and implementing robust software, Westfalia minimized the risk of future downtime. The retrofit process was completed quickly, allowing Empirical to avoid extended disruptions and costly delays.
The automation reduced manual handling, allowing employees to focus more on strategic tasks. The improved system also meant that fewer workers were needed for the picking process, contributing to operational cost savings.
Results
The retrofit project was a resounding success, turning a struggling system into a highly efficient automated warehouse. Key outcomes included: