Overview
As a prominent distributor in New Jersey’s competitive beverage industry, Allied Beverage Group faced significant operational challenges. Managing multiple warehouse locations and relying on manual processes created inefficiencies and hindered their ability to meet customer demands effectively. To address these issues and improve their operational framework, Allied sought Westfalia’s expertise. The objective was to modernize their warehouse management system through advanced automation and strategic consolidation, thereby optimizing overall performance and service quality.
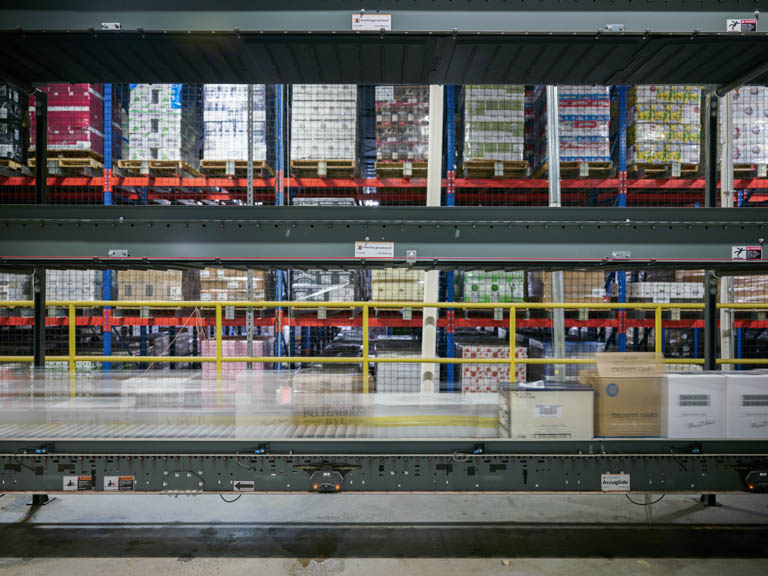
Challenge
Before the engagement with Westfalia, Allied Beverage Group struggled with labor-intensive manual processes and the complexity of coordinating operations across four distinct warehouse locations. This fragmentation led to inefficiencies in inventory management and order fulfillment, exacerbating difficulties in meeting customer expectations. The absence of a robust warehouse management system further compounded these challenges, making it difficult for Allied to track inventory and manage operations effectively.
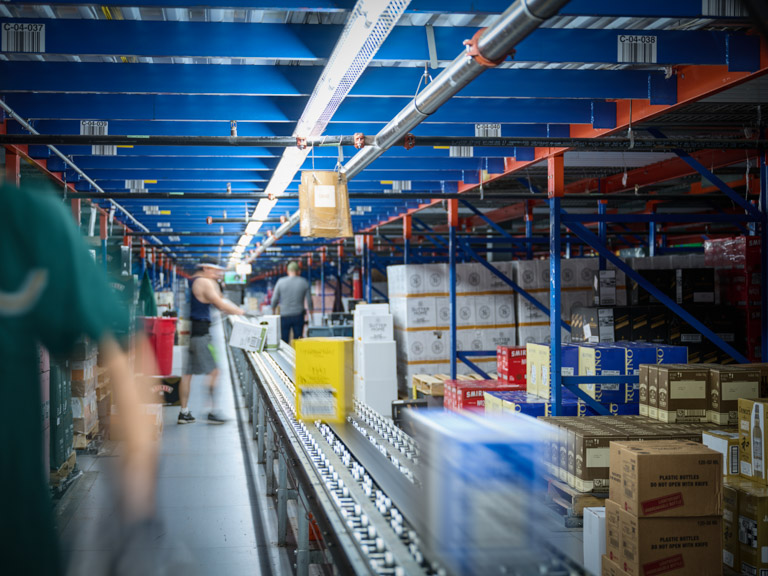
Solution
To resolve these challenges, Allied Beverage Group partnered with Westfalia to implement a comprehensive automation solution. Westfalia’s high-density storage systems and advanced automation technologies facilitated the consolidation of Allied’s warehouse operations into a single, streamlined facility. The deployment of an Automated Storage and Retrieval System (AS/RS) and Westfalia’s Savanna.NET® Warehouse Execution System (WES) transformed the warehouse into a highly efficient hub. This solution addressed Allied’s needs for improved inventory management, order fulfillment, and overall operational efficiency.
System Features
AS/RS Footprint: 180,900 sq. ft.
31,904 pallet positions
4 aisles servicing: 6-deep and 8-deep reserve storage lanes
4 tandem-pallet Satellite® S/RMs in 4 aisles, 5 levels high
Pallet conveyor systems
Automatic pallet replenishment to pallet flow pick lanes on 4 levels
Savanna.NET® Warehouse Execution (WES)
Results
The collaboration with Westfalia brought substantial improvements to Allied Beverage Group’s warehouse operations. The automation technologies implemented reduced manual labor and transportation costs while significantly boosting warehouse efficiency. Enhanced inventory tracking and faster order fulfillment led to improved customer satisfaction.