Overview
FAGE USA Dairy’s entry into the US market was highlighted by the launch of its first yogurt manufacturing plant in Johnstown, NY. In collaboration with Westfalia Technologies, FAGE implemented a sophisticated high-density automated storage and retrieval system (AS/RS) and the Savanna.NET® Warehouse Execution System (WES). This advanced system not only optimized storage and picking operations but also supported the plant’s sustainability goals with energy-efficient practices, setting a strong foundation for scalable and efficient operations.
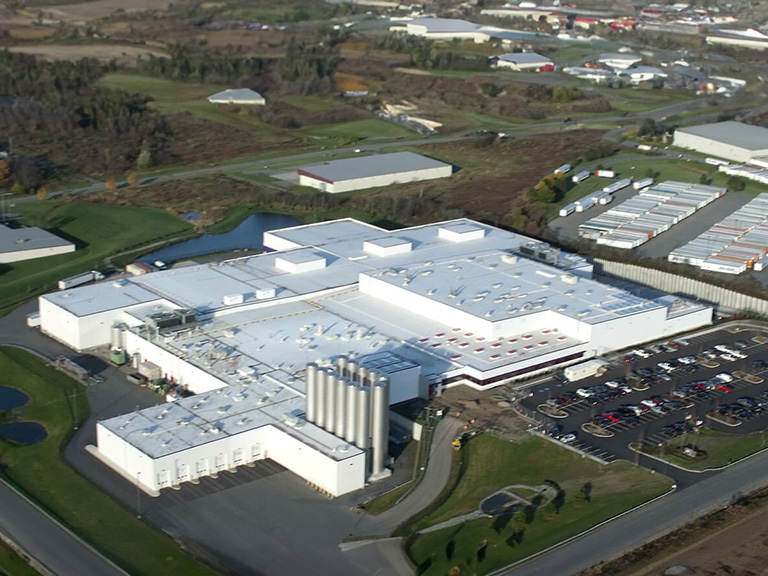
Challenge
FAGE faced the significant challenge of establishing a high-performance storage and picking infrastructure for their first U.S. yogurt manufacturing plant. The warehouse, designed with a 33’ height, needed to accommodate a diverse range of products and various order types. To meet these needs, FAGE required an advanced AS/RS solution capable of managing buffer product storage, full pallet movements, and outbound order fulfillment with a case-picking system. The system also needed to allow for the assembly of mixed-SKU customer order pallets.
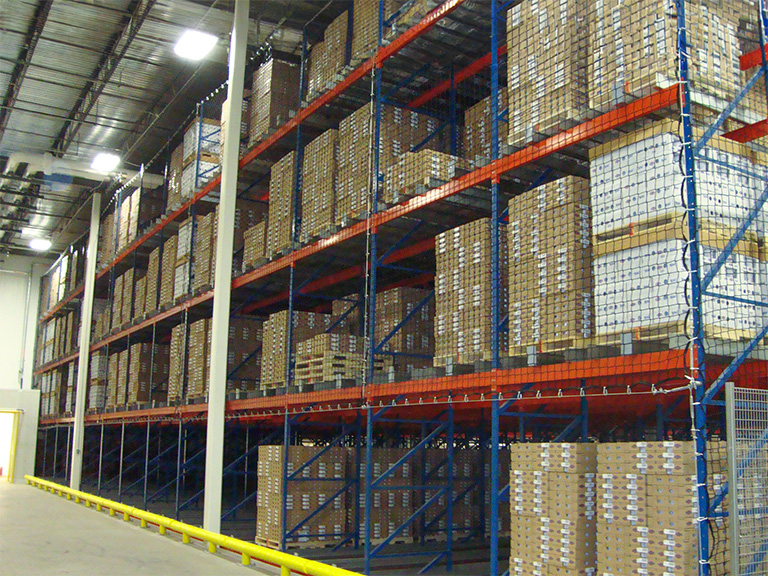
Solution
To address FAGE’s complex storage and outbound order-fulfillment requirements, Westfalia designed and implemented a state-of-the-art solution featuring a high-density AS/RS system within a 1,600-pallet free-standing rack warehouse. This advanced setup initially included one Storage/Retrieval Machine (S/RM), a complete pallet conveying system, gravity flow pick lanes, barcode scanners, stretch wrappers, and the Savanna.NET WES. These components worked in unison to create an efficient and seamless product flow within the facility.
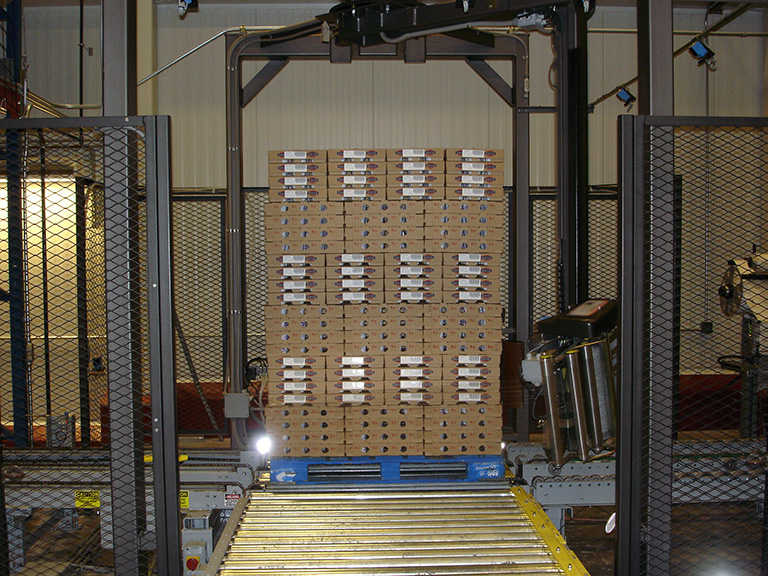
System Features
AS/RS Footprint: 56,500 sq. ft.
Initial Capacity: 1,600 pallets, serviced by (1) S/RM
Expanded Capacity: 10,124 pallets, serviced by (2) S/RMs.
Storage: 5-deep and 11-deep storage lanes x 4-levels high.
Gravity Flow Lanes: Located at floor level to support case-picking operations.
Pallets are not stretch-wrapped as they are conveyed, stored & retrieved within the AS/RS, allowing efficient cooling and case-picking operations, while eliminating waste.
AS/RS directly tied to palletizing
2 Satellite Storage/Retrieval Machines (S/RMs) in 1 aisle, 4 levels high
Pallet Conveying System
Gravity Flow Pick Lanes
Accumulation Conveyor System
Savanna.NET® Warehouse Execution System (WES): Modular WES controlling product flow, order picking, and pallet tracking.
Results
The implementation of Westfalia’s high-density AS/RS and Savanna.NET® WMS brought significant benefits to FAGE USA Dairy, including a 40% increase in storage capacity and a 30% reduction in energy costs, showcasing remarkable operational efficiency and sustainability. The system enhanced picking efficiency, automated the replenishment of picking lanes, and improved product tracking, contributing to increased productivity and reduced waste. As FAGE continues to expand in the US market, this scalable and adaptable infrastructure provides a strong foundation for ongoing success and growth.
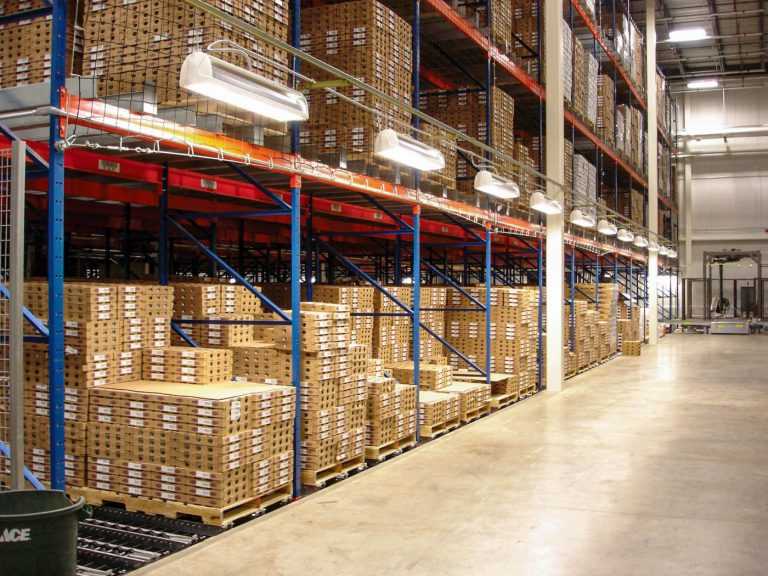