Overview
Pepsi Bottling Group (PBG), located in Tampa, FL, faced increasing product demands and operational inefficiencies. To maintain market position and meet customer needs, they needed a solution to maximize storage capacity, boost operational efficiency, and support peak production times. PBG selected Westfalia Technologies Inc. for their proven expertise in automated storage and retrieval systems (AS/RS).
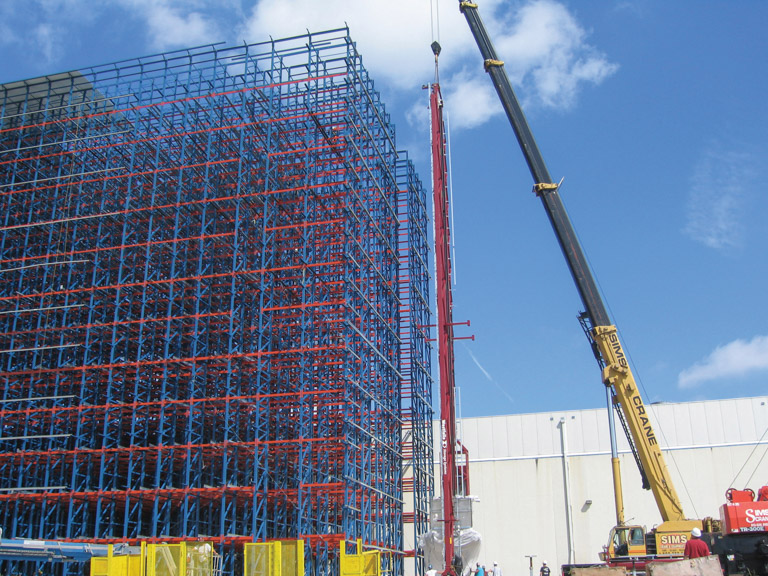
Challenge
Pepsi Bottling Group (now PepsiCo) was navigating a significant operational challenge due to escalating product demands. The key issues they faced included insufficient storage capacity, operational inefficiencies, and scalability concerns. Their existing facilities could not accommodate the growing volume of products, leading to overcrowded warehouses and difficulties in managing inventory effectively.
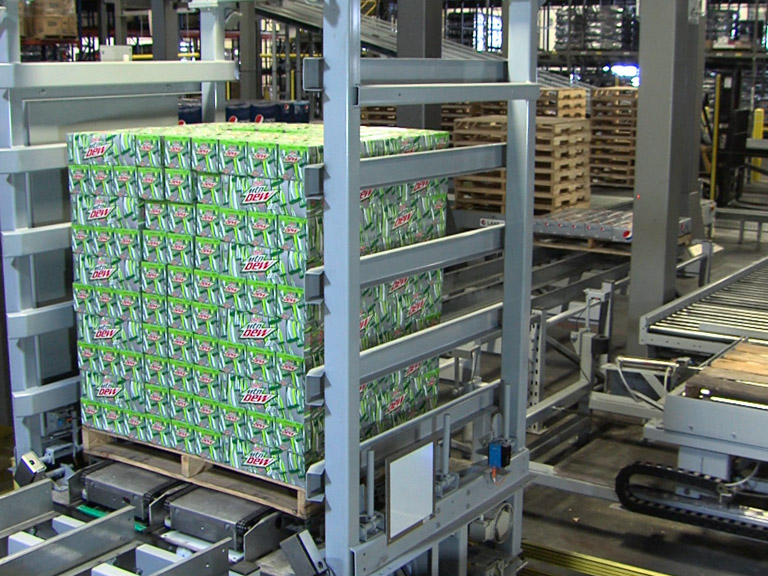
Solution
Westfalia provided a comprehensive solution for Pepsi Bottling Group (now PepsiCo) by implementing a High-Density AS/RS and Savanna.NET® Warehouse Execution System (WES). This high-density AS/RS optimized storage space, enabling efficient handling of peak production and preparation of various types of pallets for shipment. The Savanna.NET® WES managed all product flows throughout the facility, seamlessly integrating with existing systems to create a cohesive platform for warehouse operations.
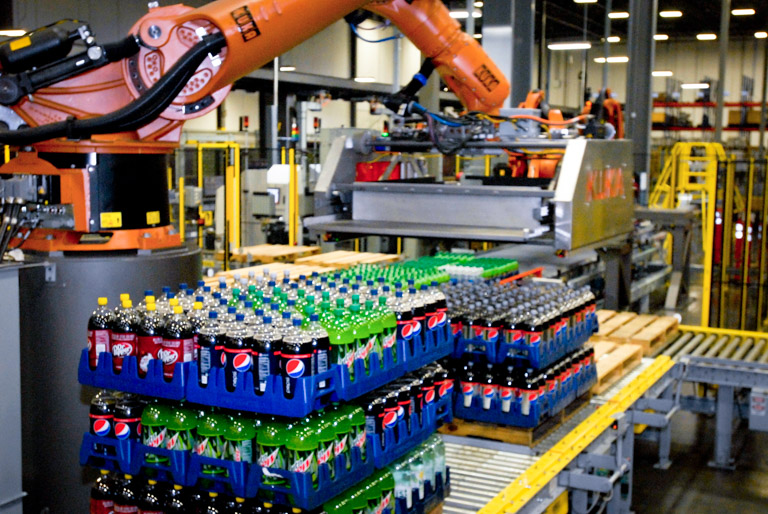
System Features
AS/RS Footprint: 27,041 sq. ft.
Number of aisles: 1
AS/RS pallet storage: 14,000 positions
2 Satellite® SR/Ms in 1 aisle, 13-levels high
Integrated with KUKA full layer palletizing and mixed layer palletizing robots
Savanna.NET® Warehouse Execution System (WES) integrated into existing ERP and WMS
Results
The implementation of Westfalia’s solutions led to significant improvements and benefits for Pepsi Bottling Group (now PepsiCo). Automation streamlined operations, enabling them to handle higher volumes of products more efficiently. By automating key processes, they reduced their reliance on manual labor, leading to cost savings. Automated systems improved precision and accuracy in product handling and order fulfillment, reducing the incidence of errors. The new systems supported their commitment to sustainability by reducing energy consumption and optimizing resource use.