9 Warehouse Problems and Solutions
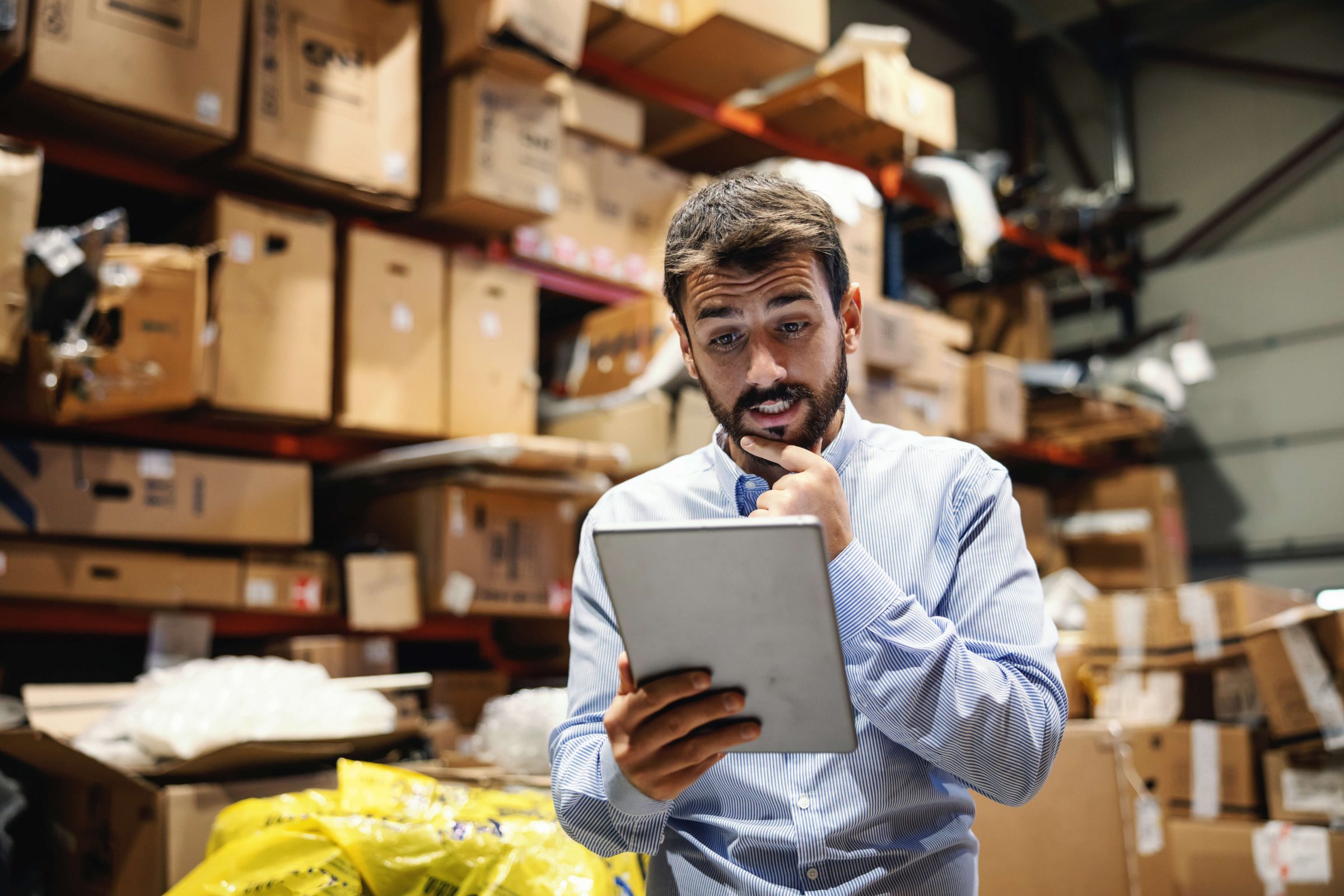
This article was updated from its original version, first published on November 15, 2019.
To outsiders, warehousing often looks straightforward—store products on racks until they’re needed—but industry insiders know it’s far from simple. Managing inventory has always been challenging, and the rapid rise of e-commerce and shifts in logistics management make it harder every day. Fortunately, technology is offering powerful solutions to streamline operations and reduce errors.
Here’s a look at nine common warehouse problems and modern solutions to help improve efficiency and reduce costs:
1. Inaccurate Inventory
Incomplete or inaccurate records reveal themselves when a worker tries to retrieve a product from an expected location, only to find it missing, or when they’re directed to store a product in a full location. Time and effort are wasted correcting errors, leading to delayed shipments and mis-picks.
Many of these issues result from inefficient, manual processes that produce inaccurate data. The solution lies in automating data recording activities with Warehouse Execution Systems (WES), Warehouse Management Systems (WMS), or other integrated systems to track real-time inventory levels and minimize errors.
2. Redundant Activities
Excessive product handling is common in many warehouses, with cases or pallets moved through several immediate locations before reaching their final destination. Sometimes, redundancy is less obvious, like duplicate data entry, which can be a significant timewaster.
To reduce these activities, start by asking your team for ideas on streamlining processes. Additionally, consulting with warehouse technology specialists can uncover opportunities for improvement. Whether it’s a new layout or investing in modern WES or robotics, there are solutions to remove unnecessary steps.
3. Suboptimal Picking
Inefficient picking wastes both time and money. Efficient picking minimizes movement, maximizing units picked per hour. Automated systems, such as an AS/RS, can significantly improve this by reducing the amount of travel required during picking.
Additionally, failing to leverage real-time data can lead to further inefficiencies, such as double handling or incorrect picks. Solutions include standardizing pick routes, integrating automation, and implementing technology to improve data handling and inventory management.
4. Poor Layout/Space Utilization
Space utilization has taken on new urgency with the rise of e-commerce. Fulfillment centers face higher picking demands, making poor layouts costly in terms of both time and space. This is especially true in urban locations where warehouse space is expensive.
Using data from a WES, you can identify the most frequently picked items and reorganize storage to minimize travel distances. Additionally, high-density storage solutions, such as AS/RS, can optimize vertical space, significantly increasing storage capacity while reducing operational costs.
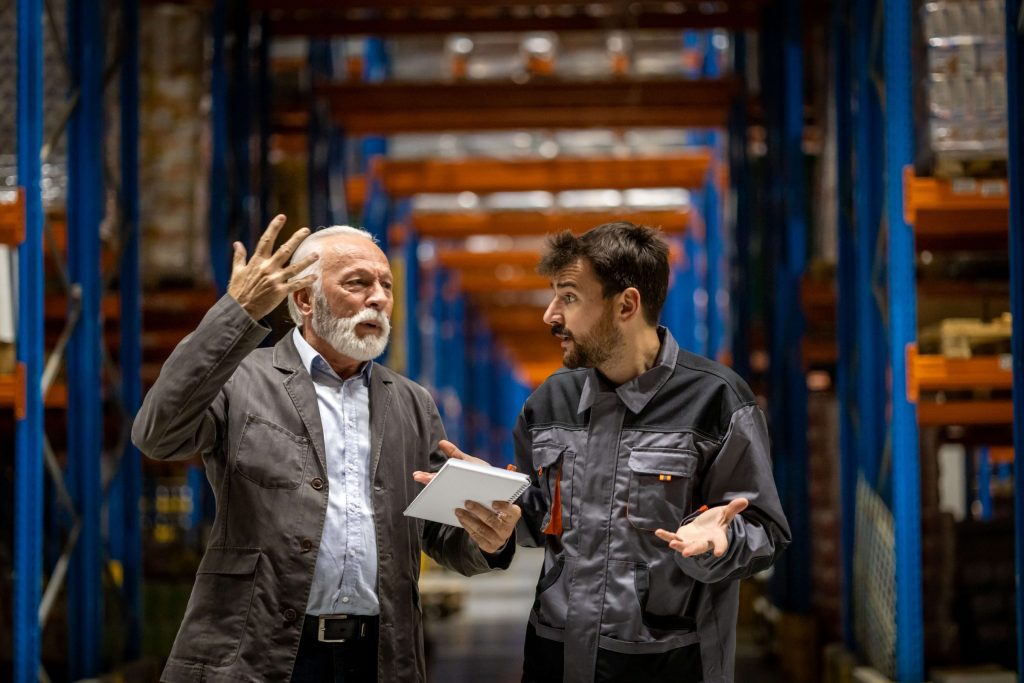
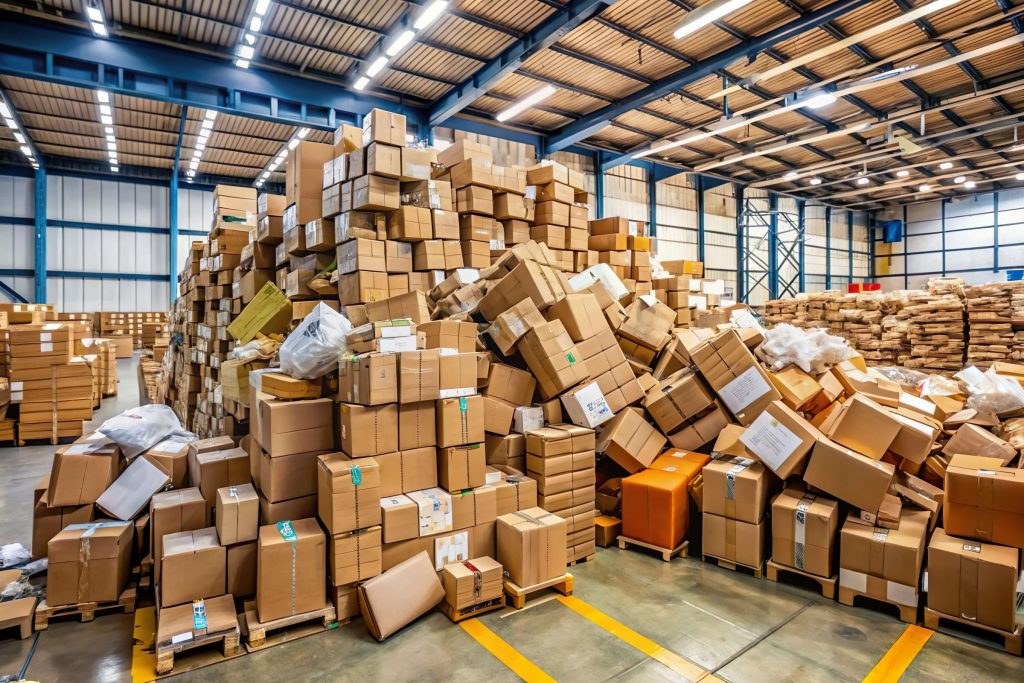
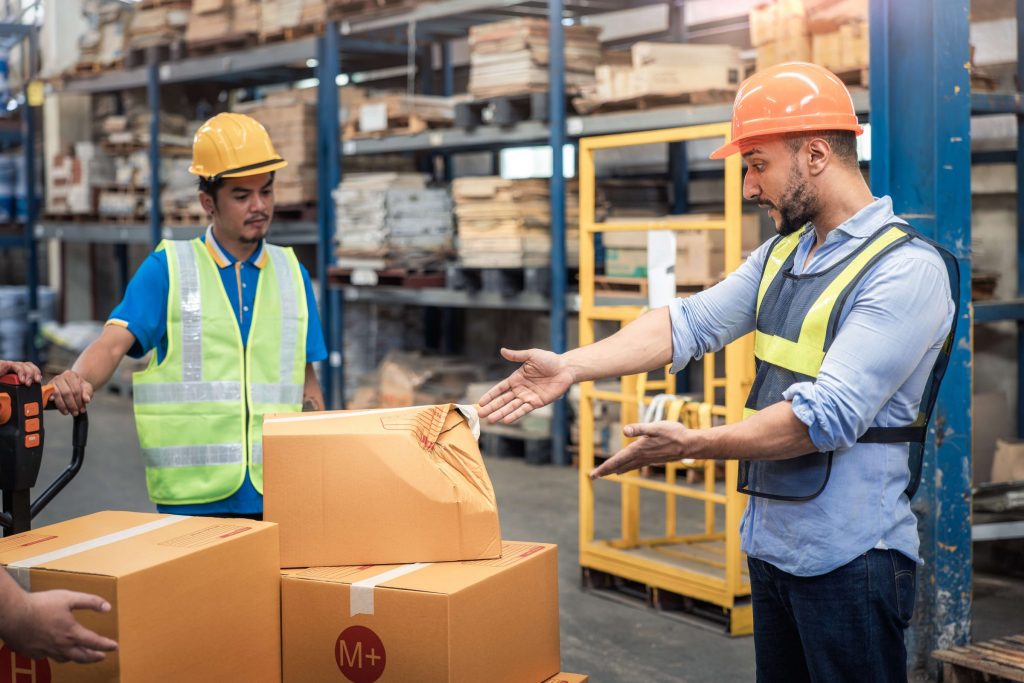
5. Product Diversification
With the growth of e-commerce and fulfillment centers, warehouses now hold a wider variety of items. While the capacity of WES systems is not typically an issue, increased product variety adds complexity to picking operations.
WES systems can help optimize storage algorithms and pick paths to manage the diversification of products. An AS/RS can also be a game-changer by automating the storage and retrieval of a wide variety of items, reducing labor costs and improving efficiency.
6. Seasonal Demands
Seasonal fluctuations in demand pose a significant challenge in warehousing. Configuring the warehouse for peak periods can lead to underutilization during slower months, affecting profitability.
Warehouse automation systems can help mitigate these fluctuations. Solutions like pallet flow systems, advanced racking, and AS/RS can boost units handled per hour, providing the flexibility to scale up during peak seasons without wasting space in quieter times. Modern automation allows businesses to remain efficient year-round.
7. High Labor Costs
Warehouse managers are increasingly pressured to reduce labor costs while maintaining or improving service levels. Labor shortages, worsened by the pandemic, have driven many warehouses to seek automated solutions.
While picking is still largely manual, emerging technologies such as autonomous mobile robots (AMRs) and AS/RS can complement human labor, speeding up picking processes and reducing overall labor costs.
8. Avoiding Product Damage
Product damage can occur at multiple points in the warehouse, often during picking or transport. Damaged items lead to lost revenue and customer dissatisfaction.
New racking and pallet flow systems can reduce damage by carefully controlling product movement. Zero pressure systems, for example, prevent product collisions by maintaining separation. Automated systems such as AS/RS ensure precise handling, further reducing the risk of damage.
9. Handling Returned Items (Reverse Logistics)
Returns processing has grown significantly with the rise of e-commerce. Poorly planned systems lead to double handling, wasted time, and poor record-keeping, which ultimately increases costs.
Start by documenting the returns process, identifying bottlenecks, and standardizing procedures. Automation solutions, such as dedicated return handling systems and a WES, can streamline reverse logistics, improving efficiency and tracking accuracy.
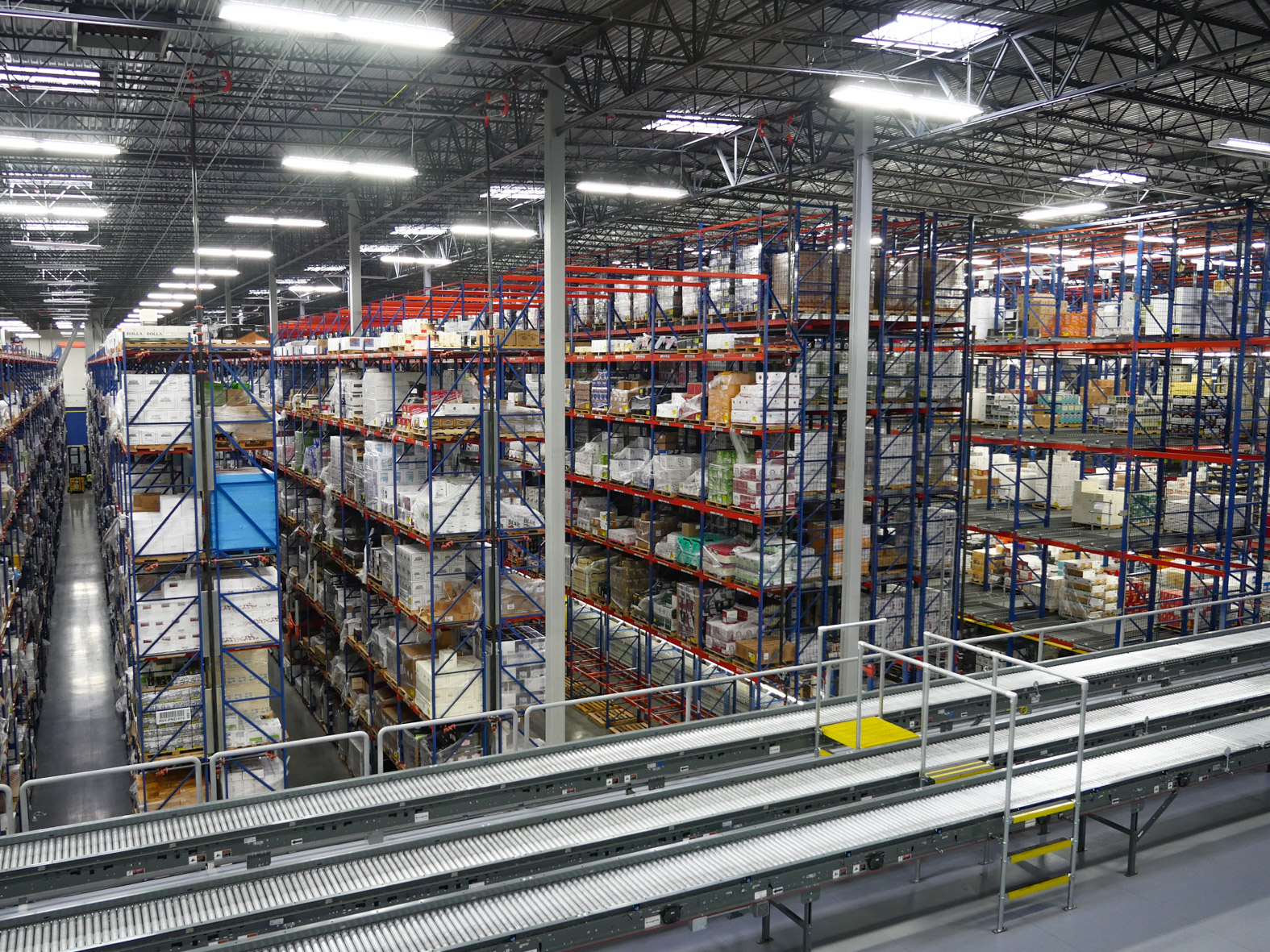
Industry Appropriate Solutions
Warehouse challenges vary by industry, so there’s no one-size-fits-all solution. At Westfalia Technologies, we tailor solutions to the specific needs of each client. Whether it’s implementing AS/RS, optimizing your WES, or designing better pallet flow systems, we help businesses in industries like food and beverage distribution, 3PL, and more overcome their warehouse problems and achieve operational excellence.